Aglutinante, cemento o yeso se utiliza como parte de la regla, el relleno es de arena de diversas fracciones, aditivos minerales y polímeros proporcionan propiedades mejoradas de la mezcla. El agua de reproducción de estos componentes proporciona la solución de consistencia requerida.
Las soleras de cemento no temen a la humedad. Se pueden utilizar en la construcción de suelos en cualquier habitación. Se pueden utilizar mezclas de cemento y arena preparadas manualmente (tradicionalmente en una proporción de 1:3) u hormigón de arena especialmente preparado (se venden mezclas preparadas). Hay que tener en cuenta que estas mezclas presentan una contracción importante. Por tanto, pueden aparecer grietas si se colocan mezclas desiguales o capas de grosor inferior a 30 mm. Se producirá el enrasado de la base. El enrasado en solución o el uso de una malla de refuerzo dentro de la capa de fibras de propileno garantiza una distribución uniforme de la tensión y evita la aparición de grietas. Además, para un curado uniforme, se recomienda humedecer regularmente la solera de cemento fresco durante varios días. Se seca durante mucho tiempo y es demasiado húmedo para colocar suelos sensibles a la humedad durante al menos 20 días (parquet, laminado).
La solera de yeso (angindride) es plástica, fácil de ejecutar, se seca en 24-48 horas, no se contrae en absoluto y puede colocarse en capas finas. Sin embargo, este tipo de solado no es adecuado para suelos de estancias húmedas, ya que el yeso absorbe la humedad.
Tanto las soleras de cemento como las de yeso se venden en forma de mezclas secas. Contienen aditivos modificadores que simplifican el amasado, aumentan la fluidez, facilitan la colocación de la solución, aplanan la superficie, reducen la retracción, aceleran el curado de la solera y eliminan el agua inmediatamente. Cuando se utilizan mezclas secas, no es necesario reforzar la capa. Puede colocarse mecánica o manualmente. El tiempo de secado, el método de colocación y la idoneidad de la solución para trabajar tras la dilución indican el envasado.
Las soleras hechas con soluciones secas sin diluir deben reforzarse por encima con una capa de cemento o yeso
También se producen mezclas secas para insertar calor, que incluyen rellenos especiales como perlita, cerámica y espuma de poliestireno. El uso de solado «caliente» proporciona aislamiento térmico, aislamiento acústico y alineación de la superficie al mismo tiempo. Sin embargo, por regla general, debe reforzarse con una capa de cemento o yeso.
Las soleras «secas» son las más rápidas de fabricar y todo el trabajo relacionado con la instalación del suelo puede realizarse en un solo día. Para ello se utilizan DVP, tableros de aglomerado, placas de yeso o placas especiales de yeso. También existen placas multicapa para solado en seco. Éstas contienen una capa de aislamiento de láminas y paneles de yeso rodeada de humedad. Esto proporciona simultáneamente aislamiento hidráulico, térmico y acústico, resistencia y rigidez. Este tipo de placas han aparecido recientemente en el mercado ucraniano y aún no se han distribuido.
La mezcla de los cimientos, tanto de yeso como de cemento, se divide en alineadora y autoniveladora.
La mezcla de nivelación está diseñado para la alineación gruesa de la base y elimina los cambios y las crestas — solado negro. Después de la cría de agua debe tener una consistencia espesa y puede poner en capas gruesas (hasta 100 mm). Capas siguen las reglas, pero es difícil conseguir una superficie perfectamente plana.
Las mezclas autonivelantes (masas nivelantes) están diseñadas para crear una superficie acabada plana y ya pueden colocar incluso los suelos más quisquillosos. Se diluyen con agua hasta conseguir la consistencia de un líquido que se vierte sobre el suelo. Las mezclas autonivelantes también están disponibles en dos tipos: capas finas (de 2 a 7 mm de grosor) y gruesas (de 5 a 30 mm de grosor). Debido a las importantes irregularidades de la base y a las grandes diferencias en su altura, es mejor hacer la solera en dos fases. En primer lugar, la base se alinea aproximadamente a la altura requerida y, a continuación, se crea una fina superficie ideal de mezcla autonivelante.
Tabla
- Torres de madera.
- Consejo de expertos.
- Determinar el grosor de la solera
- Consumo de la mezcla de cemento y arena
- Breve programa didáctico, o qué solado se necesita
- Soleras semisecas.
- Objetivo.
- Instrucciones paso a paso para aplicar la solera de alineacion
- Tipos de soleras de cemento
- Herramientas y materiales
- Cálculo del número de materiales necesarios para el enrasado.
Torres de madera.
No es aconsejable colocar solado de hormigón sobre suelos de madera, ya que la considerable masa de la losa monolítica crea una gran carga sobre la base. Al mismo tiempo, la humedad presente en la mezcla durante el curado puede tener un impacto negativo en la madera.
Sin embargo, puede que no haya alternativa a esta opción y que las soleras de hormigón, las tablas, los fanners o los tableros OSB sobre suelos de madera sean el único camino a seguir.
Las soleras están prohibidas en las nuevas construcciones de madera debido al alto potencial de deformación por contracción significativa. Esto es especialmente cierto en el caso de las operaciones de al menos tres o cuatro años debido a la contracción completa de la madera, desde el género y las tablas del suelo hechas a lo largo del calorifugado. En el caso de las placas de madera contrachapada y OSB, este factor no es importante, ya que no hay contracción en materiales especialmente tratados.
Antes de realizar la mezcla de hormigón sobre una base de madera, todas las estructuras deben tratarse con un compuesto conservante. Hay que desmontar el suelo y sustituir los retrasos que haya que reparar. Si el diseño no es lo suficientemente fiable, debe reforzarse mediante la instalación de barras adicionales.
Los peldaños de la alfombra deben ser de 30-40 cm. Esto proporciona suficiente capacidad de soporte para la base de madera. Después de la instalación inversa del suelo, se cubre con una composición hidrófoba y las grietas entre las tablas o contrachapado se sellan con un sellador impermeable.
La madera puede cambiar sus dimensiones geométricas durante el funcionamiento cuando cambian los regímenes de humedad, y las soleras de hormigón son en su mayoría estables. Por eso, la técnica de verter hormigón sobre una base de madera consiste en crear un límite de separación entre las capas: un dispositivo de suelo «flotante». De lo contrario, la movilidad del suelo de madera podría provocar la destrucción de la solera de hormigón.
Para ello, las placas monolíticas se cortan a lo largo del perímetro con cintas amortiguadoras y el hormigón y la madera se separan con material de cubierta, papel pergamino o masilla bituminosa, pero es mejor hacer una capa de película de polietileno, porque hay cero La unión entre el hormigón y la plancha «se desliza» libremente.
La cinta amortiguadora de espuma de poliestireno debe colocarse 2-3 cm por encima del nivel de la futura solera. El exceso se retira y se cierra con zócalo. El polietileno se cubre con un solape de 10-15 cm y penetra en la pared hasta la altura de la cinta amortiguadora. De este modo, se crea una «depresión» impermeable en la superficie del suelo de madera y se coloca la mezcla de hormigón.
Deben evitarse las perforaciones aleatorias de la lámina impermeabilizante. En el caso de formaciones, deben sellarse con cinta adhesiva. Por lo tanto, la estructura no se puede utilizar para tornillos autorroscantes para instalar faros.
Para reducir el peso de las losas monolíticas, se recomienda utilizar tipos de hormigón más ligeros, con un peso específico de 800-1200 kg/m3 . Con un espesor de 5 cm, la carga por m2 es de 40-60 kg.
Estos tipos incluyen.
- Hormigón de escoria;.
- Hormigón Pamzon; y
- Keramziton.
Además, estos compuestos tienen unas propiedades de aislamiento térmico y acústico mucho mayores.
En el futuro, la técnica de instalación de la solera de hormigón sobre una base de madera será similar a la colocación de la mezcla sobre un forjado. La excepción es su refuerzo. Para reducir la carga sobre la base de madera, se recomienda utilizar fibras de polipropileno o rejillas de plástico en lugar de refuerzo.
Las soleras reforzadas de este modo pesan menos, pero no son menos resistentes que las bases con malla metálica. En los suelos de madera puede colocarse una capa adicional de aislamiento acústico y térmico. Se puede instalar un sistema de «suelo caliente».
Si se utilizan métodos de calefacción eléctrica, la base de madera debe tratarse con un antiincendios. El cuidado de la base de hormigón durante el proceso de curado no difiere del estándar.
Consejo de expertos.
Los expertos aconsejan prestar atención a los siguientes consejos
- Cuando se planifique un acabado con una mezcla autonivelante, debe disponerse de una superficie perfectamente plana. No es necesario conseguir un brillo en la mezcla a granel, ya que las partículas gruesas de arena no pueden atravesar el suelo en una capa ideal. Siempre hay una base ligeramente gruesa.
- No debe permitirse un exceso de agua en la solución. Al principio, cuando se coloca, la mezcla de agua parece perfecta, pero luego da una fuerte contracción. La superficie será irregular. Las grietas aparecen con el exceso de agua y es necesario alisarlas con una nueva porción de la mezcla durante más tiempo.
- Durante la operación, las ventanas deben cerrarse con cortinas para que la luz solar directa no incida sobre la solución inundada. Las puertas no pueden abrirse para evitar corrientes de aire.
- Mientras pueda caminar (3-5 días), durante el conjunto de intensidades, debe excluirse el movimiento de personas y animales domésticos a lo largo del mismo.
- Los faros deben ser retirados después de 2-3 días, no inmediatamente al final del trabajo. Las zanjas identificadas se limpian con los restos de la mezcla preparada.
- El secado completo se produce después de aproximadamente 28-30 días. No comience el acabado del suelo antes de la expiración de este período.
Realizar el solado en un piso con sus propias manos no es difícil. Para ello, es necesario estudiar las instrucciones, calcular los volúmenes, elaborar un esquema de trabajo y preparar todas las herramientas y materiales necesarios.
Se recomienda ver el vídeo con instrucciones paso a paso para jugar solado en un piso.
Determinar el grosor de la solera
En esta fase, hay que determinar el grosor de la solera. Para ello, medir la base a través del área para encontrar el promedio de la diferencia entre el punto más alto y la marca.
Parto del hecho de que la solera es necesaria como capa de nivelación y no ayuda a bloquear la comunicación.
En el punto más alto de la base, el espesor de la solera debe ser mínimo para ahorrar material y reducir la carga sobre el forjado.
El espesor mínimo admisible de la solera de cemento y arena al colocar la mezcla sobre una losa de suelo o una base de hormigón es de 20 mm (según SP 29. 13330. 2011 «Suelos»). Sin embargo, muchos constructores recomiendan mantener un valor de 30 mm. Esto significa que es difícil de observar en casa, refiriéndose al hecho de que los documentos normativos discuten las condiciones ideales y las proporciones del material.
Así, en el punto más bajo de la base, el espesor de la capa será el más alto.
Lo más conveniente es realizar mediciones y marcas con un nivel láser, también llamado nivel láser.
Merece la pena decir unas palabras sobre el principio de funcionamiento de este dispositivo.
El nivel láser proporciona una superficie estrictamente horizontal que se proyecta en forma de líneas láser horizontales sobre la pared. Algunos modelos pueden proporcionar además dos planos verticales mutuamente perpendiculares.
Esquemas de cimentación de suelos mediante nivel láser y ruleta. Cuanto más alto es el punto, más baja es la escala de medición y viceversa.
Para las mediciones pueden utilizarse ruletas, carriles de nivelación o niveles de construcción de escala milimétrica. El esquema anterior muestra que cuanto más alto esté situado el punto base, mayor será la lectura de la ruleta y viceversa, cuanto más alto sea el punto, más baja será la marca.
El nivel láser debe colocarse en el centro de la habitación, encenderse, colocar la ruleta o el carril de nivelación en el punto especificado y retirar y anotar las lecturas de la escala.
Esquemas de suelos utilizando un nivel láser
Las mediciones se realizan a intervalos de 1,0 a 1,5 metros y en puntos característicos, es decir, donde las gotas de las marcas son claramente visibles visualmente.
Lo más conveniente es crear un esquema de medición y aplicar sobre él los resultados obtenidos.
Ejemplo de esquema básico de cimentación con resultados. Punto 16 — Características.
A continuación, hay que procesar los resultados. Para ello, cree una tabla.
En la tabla se puede ver que los puntos más altos de la base son los nº 12, 14 y 15 y el más bajo el nº 16.
A continuación, resta el valor del punto más alto (15 cm) de las marcas de todos los puntos y anota la diferencia (véase la columna 3). Esto significa que la tercera columna tiene un exceso del punto más alto sobre todas las demás columnas. Por ejemplo, el punto nº 12 (y 14 y 15) está 1,5 cm por encima del punto nº 8.
El espesor mínimo admisible de la solera debe sumarse entonces al valor de la tercera columna. Como en el caso anterior, si la solera de cemento y arena se coloca sobre una placa solapada o una base de hormigón, el espesor mínimo de la capa es de 20 mm, por lo que en la cuarta columna se toma el espesor de la solera en cada punto.
A partir de estos datos, puede calcularse el espesor medio de la solera. Para ello, se resume el espesor de la solera en cada punto y se divide por el número de puntos. En este ejemplo, se obtienen 3,0 cm.
El valor medio del grosor de la regla se necesita para calcular el número de materiales para la preparación de la solución, en lugar de prestar atención al siguiente paso.
Al ejecutar el dispositivo de solado, es importante recordar que hay que tener en cuenta la carga calculada sobre el forjado y no superarla. Para ello, es necesario consultar los datos del proyecto sobre el que se construyó la casa
Por regla general, una solera de 5 cm de grosor no es crítica, pero conviene aclarar este momento. Para la instalación de soleras gruesas, se utiliza material poroso a granel (arcilla expandida) como relleno en solución u otra capa de cimentación
Consumo de la mezcla de cemento y arena
Tabla 4: Composición de la mezcla y consumo de componentes
La mezcla se consume en función del tipo de obra y del espesor de la capa aplicada. Para un cálculo exacto del material utilizado, se puede hacer una muestra de prueba y comenzar con un indicador.
Para las cubetas de solado.
Para calcular la cantidad de material para la solera, es necesario encontrar el cubo de solución utilizado para la bahía. Para ello, es necesario multiplicar el suelo por el espesor de la capa. Por ejemplo, el tamaño de la solera rara vez supera los 30 cm. Por ejemplo, si en una habitación el suelo se rellena con una solera de 10 cm de grosor, 100 m2 requerirán 10 metros cúbicos de solución. Su preparación requiere 555 para 713 kg de mezcla seca (según la marca).
Cuanto mayor sea la marca de la mezcla, mayor será la densidad: para preparar un cubo de solución a partir de una mezcla de M100, se necesitan 550-600 kg o 700 kg de mezcla I 32. 5N GOST 31108-2016 (marca M400).
Mezcla semiseca para solado.
Las mezclas semisecas pueden utilizarse para la producción de soleras. Las mezclas duras (semisecas) se distinguen por su reducido contenido de agua. Además de cemento, arena y agua, la composición de estas mezclas incluye fibras, plastificantes y, en caso necesario, aditivos anticontrol. Mediante un dispositivo especial equipado con una bomba, se hace pasar por la manguera un suministro de la mitad de la mezcla. El faro se fabrica con la media mezcla y se produce el relleno.
Ventajas de la media mezcla:
- Ejecución de la regla en una sola cita.
- Solidificación rápida;.
- Reducción de la contracción y la formación de grietas.
La media solera de humo es un proceso de alta tecnología que puede mejorar la calidad del trabajo.
Solado húmedo.
Hecho de mezcla de cemento y arena de la marca M150-300. La mezcla seca se cierra en el lugar con agua. La superficie para el relleno se impriman previamente. La imprimación forma una fina película que aumenta las propiedades de adherencia. La película de tierra retiene la humedad en la solera.
Coeficiente de conductividad térmica de las soleras de cemento y arena
La conductividad térmica de las soleras depende de la relación cemento/arena. Las soluciones normales de cemento y arena tienen un coeficiente de conductividad térmica de 1,2 w/m*k. Esto significa que el material tiene una alta conductividad térmica y una pérdida de calor significativa, es decir, el suelo es más frío y necesita más medios para calentarse.
La conductividad térmica de la solera durante los cálculos de ingeniería se selecciona a partir de una tabla de referencia en la que se da un indicador en función del material utilizado. La conductividad térmica de los materiales estructurales y de aislamiento térmico es de 0,02-2,1 w/m*k y depende de la temperatura (aumenta al aumentar la temperatura). Crece a medida que aumenta la densidad del material, pero la presencia de cavidades, poros y capas de aire hace que el material no pueda considerarse homogéneo. A medida que la conductividad térmica del gas se sitúa en el intervalo 0,004-0,4 w/m*k, la densidad total disminuye. En este caso, se reduce la transferencia de calor y disminuye el coeficiente de conductividad térmica de la solera.
La arcilla expandida o la perlita hinchada pueden utilizarse como relleno aislante térmico para reducir la conductividad térmica de la solera, pero cuanto mayor sea el relleno, menor será la resistencia de la solera. Además, los rellenos grandes complican la formación de una superficie de solado plana.
Para paredes con relleno
Como las paredes no son uniformes, con salientes, cavidades y huecos, casi siempre se puede determinar el consumo de material.
Por tanto, el cálculo determina la profundidad media de las capas.
Las capas de yeso tienen un espesor de 5-30 mm. A menudo se añade cal a la solución de yeso para reducir el consumo de CPS.
El grosor de la capa es de 10 mm y el consumo de mezcla M400 por m2 es de 1,6 kg y M500 — 1,4 kg.
Para ladrillos de mampostería
Para las operaciones de albañilería se utiliza una mezcla de M100 o M200. Para 1 m3 de mampostería se necesitan 250 g de CP seco.
Es necesario aclarar los datos de la documentación reglamentaria.
Formas de ahorrar CPS
Para reducir el consumo de CPS, se utilizan rellenos.
- Arcilla expandida para reducir la conductividad térmica de la viga de solado.
- Solución de cal para el enlucido.
Además, se puede utilizar cemento de alta máscara reduciendo la cantidad de mezcla o agrupando los cimientos para reducir el flujo de la solución.
Breve programa didáctico, o qué solado se necesita
Antes de plantear la cuestión de cómo hacer un solado, hay que ponerse de acuerdo sobre las condiciones. Es habitual referirse a la solera como una capa de mezcla estructural. Se coloca entre la base del suelo y el suelo acabado. Esta capa desempeña las siguientes funciones clave
En función de la composición de la mezcla y del método de peinado, se distinguen varios tipos de solado.
El mortero de cemento y arena es el material más utilizado para la nivelación de suelos. Las mezclas secas de producción industrial son las más habituales en la construcción.
Se fabrican a base de cemento y arena, a la que se pretende dar plasticidad y plasticidad, fibras de fibra y otros componentes que mejoran las propiedades de la solera.
Según el método de colocación, el solado es húmedo, seco y semiseco.
El método clásic o-húmedo- consiste en verter la base con una solución de solado con posterior solidificación.
La mezcla se coloca directamente sobre el forjado o una capa de aislamiento hidráulico o térmico. Este último requisito es esencial cuando la pantalla se instala directamente sobre el suelo (por ejemplo, en estructuras como jardines). Las capas de impermeabilización son necesarias en estancias con mucha humedad (baños, aseos).
Las soleras húmedas se utilizan cada vez más debido a sus numerosos inconvenientes.
La solera seca está hecha de material en láminas y se coloca sobre una base (por ejemplo, arcilla expandida, arena) encima de la capa aislante. Las ventajas de este método son la rapidez y facilidad de instalación y el bajo peso de la estructura. La principal desventaja de la solera seca es que no se puede utilizar en habitaciones con mucha humedad y los costes son elevados, ya que el material de la hoja tiene miedo al agua.
La media solera puede denominarse una variante mejorada del método húmedo. La composición se prepara a base de mortero de cemento y arena con fibras de fibra y plastificantes añadidos. Para la colocación se utiliza una cámara neumática. Ésta amasa los componentes y suministra la mezcla al objeto.
Las cámaras neumáticas son máquinas compresoras especiales para la preparación, amasado y transporte de diferentes composiciones estructurales.
Este método se denomina semiseco porque el contenido de agua en la solución se reduce considerablemente gracias a los aditivos. Gracias a ello, la solera es más ligera, duradera y resistente.
La solución sólo tarda 12 horas en secarse. Al cabo de unos días, la solera puede recibir un revestimiento decorativo de acabado. Este método sólo tiene un inconveniente: hay que utilizar un equipo especial.
Soleras semisecas.
Si se añaden aditivos o aditivos de refuerzo a la composición estándar de cemento y arena de la solera, se obtiene un hormigón más resistente y con menos agua. Las adiciones o aditivos aceleran el proceso de adquisición de resistencia del hormigón.
Son diferentes y confieren distintas propiedades:
- Aditivos antiácido zóico, que aceleran la maduración de la solera, al tiempo que reducen la temperatura de congelación del agua. Se utilizan cuando las temperaturas descienden por debajo de +5°C (el invierno del hormigón comienza a esas temperaturas).
- Fibra: los trozos de fibra o alambre de acero aumentan considerablemente la resistencia y la solera no se agrieta ni siquiera bajo cargas considerables.
- Para las propiedades foliares del agua. Son útiles para rellenar soleras en lavabos y vaporeras, baños, aseos o cocinas.
- Los aditivos que se autointegran con la solución, es decir, su apisonado, no son necesarios.
Las normas para añadir aditivos están pintadas en el envase. Varían entre el 0,3 y el 10% de la masa del cemento. Esto significa que hay que añadir entre 3 y 100 gramos de aditivos por kilogramo.
En la producción de soleras semisecas se necesita varias veces menos agua. En primer lugar, se mezclan los componentes completamente secos y, a continuación, se añade agua. Sin embargo, la solución debe ser como la arena mojada de la playa. Si se aprieta en la mano se acentuará un poco la humedad, pero no fluirá y quedará grumosa en la mano. Esta será la consistencia perfecta.
Debido a que este tipo de soluciones tienen menos plástico, su alineación es más problemática. Se requiere más esfuerzo. Después de colocar la configuración entre las guías, se compacta. Esto puede hacerse utilizando un vibrador de superficie especial para hormigón. Alternativamente, los pies pueden ser abrazados como se muestra en el video.
Objetivo.
Las soleras de cemento colocadas en el suelo tienen una función única
Es muy importante saber por qué son necesarias las soleras.
- Creación de una superficie de suelo plana. Falta o defectos de nivelación.
- Dispositivo de superficie de dos capas para sistemas de suelo caliente. La primera capa se coloca después de la capa de aislamiento y la segunda después de colocar la línea de calefacción.
- Colocar el suelo a un mismo nivel en diferentes habitaciones. Estos problemas empiezan a aparecer tras un vertido de hormigón de calidad insuficiente o unos niveles mal fijados. Aparte de este punto, es imposible realizar una colocación de calidad del suelo en el futuro. De lo contrario, pueden formarse los llamados «escalones».
- El suelo siempre debe soportar una carga específica y tener un nivel de resistencia suficiente. Aquí es donde las soleras vienen al rescate.
Pero éstas son sólo las funciones más pequeñas y básicas que puede desempeñar una solera de piso. Todo lo demás depende de las circunstancias específicas de su instalación.
Instrucciones paso a paso para aplicar la solera de alineacion
Descubra cómo hacer una solera de hormigón.
En primer lugar, debe establecer una marca a una altura determinada del suelo utilizando un nivel láser. Incluso el «nivel cero» de la futura solera depende de que el suelo esté uniforme y limpio. La altura óptima para el «nivel cero» es de 1,5 cm desde la superficie de la base.
Preparación de la superficie. La base debe limpiarse de pavimentos antiguos, polvo y suciedad. Todas las grietas y pequeños defectos de la superficie deben eliminarse utilizando una composición especial de reparación a base de cemento.
La superficie reparada preparada debe cubrirse con una imprimación. Se recomienda reforzar la superficie con pegado de solado, utilizando para ello tierra con arena de cuarzo.
En la junta entre el suelo y la pared, pegar cintas de componentes para separar las superficies verticales.
Utilizando trozos de perfiles de aluminio, coloque el faro y fíjelo a la base. Los faros son un requisito indispensable para obtener soleras planas y ordenadas. Instálalos utilizando un nivel, para que en el futuro puedas orientar el grosor de la capa de nivelación en función del nivel del faro.
Ver vídeo Cómo hacer soleras en pisos
Siga las instrucciones para preparar la solución de consistencia deseada. Mezcle bien la solución utilizando una boquilla mezcladora en el taladro para evitar la aparición de grumos. La mezcla debe ser homogénea y espesa.
Utilice la solución inmediatamente y sin esperar a que espese y pierda sus propiedades. La mezcla se vierte limpiamente sobre la base preparada y se nivela con un rodillo de engranajes sobre un mango largo. Esto es necesario para eliminar las pequeñas burbujas de aire de la solución, que posteriormente pueden empeorar la resistencia de la capa de nivelación.
En la actualidad, cada vez es más popular una nueva tecnología para realizar solados semisecos. Este método difiere del método habitual del abuelo en que, en este caso, la solución de cemento y arena contiene un mínimo de agua y se interviene en la obra fuera de la habitación, mientras que a la propia habitación se le suministra una solución especial a presión. A continuación, se nivela con el nivel láser, se recorta y se limpia con una máquina especial de rejuntado.
Durante el día, una brigada ejecuta una media solera de hasta 300 metros cuadrados.
En lugar de malla de refuerzo de acero, se utiliza un elemento de refuerzo, que es fibra de refuerzo HSU. Esta se introduce en la propia solución como aditivo. Y lo que es más importante, el precio de la media solera es aún más bajo que el de la «húmeda» clásica.
Solado de cemento en el suelo
Del autor: durante las reparaciones pueden ocurrir incidentes: que se acabe la arena y se despegue el papel pintado.
Para evitar este tipo de sorpresas, es importante abordar el trabajo con responsabilidad, realizar cálculos preliminares y plantearse nuevas medidas.
El solado de cemento de bricolaje no es una excepción, ya que es una de las fases de la reparación. El resultado final depende en gran medida de la calidad de su ejecución.
Tipos de soleras de cemento
En primer lugar, entendamos por qué son necesarias las soleras. La solera de hormigón es una capa de mortero de cemento y arena (con relleno) que actúa como base de nivelación negra para la posterior instalación del revestimiento de acabado.
Las soleras se clasifican en función de una serie de parámetros, como el método de instalación, las condiciones y el uso previsto. Hablando específicamente de soleras de cemento, se dividen en los siguientes grupos
- Soleras asociadas. Se trata del tipo más sencillo de revestimiento de cemento, en el que una mezcla de cemento y arena se coloca directamente sobre la losa del suelo y se cubre rígidamente para que se adhiera. Este tipo de soleras se utilizan con mayor frecuencia en la alineación en negro de las superficies de los suelos y en los pisos superiores de las casas. Aquí no es necesaria la instalación de un suelo caliente.
- Solado de capa de separación. Esta versión de la capa de separación es impermeable y se coloca para proteger el subsuelo de filtraciones. La impermeabilización también puede utilizarse si la base del relleno es un solapamiento de madera. Las soleras no se atan a la base, sino que se asocian a la pared, por lo que requieren un espesor mínimo de capa de 5 cm. Además, si se utiliza una solera de este tipo, debe reforzarse para protegerla de grietas y roturas. Además de los métodos tradicionales, pueden utilizarse fibras sintéticas como refuerzo.
- Soleras flotantes. Cuando se coloca un suelo caliente sobre una solera, debe garantizarse la protección contra las fugas de calor «hacia el suelo». Para ello, se coloca una capa de aislamiento térmico en la superficie del forjado. Por regla general, se utiliza espuma de poliestireno extruido como aislamiento térmico. Los marcos de refuerzo se fijan a la capa de aislamiento y se elevan ligeramente por encima de la superficie del suelo, donde se realiza la comunicación del sistema de suelo caliente. De este modo, tras verter la solera, se obtiene una tarima que no está unida al forjado ni a las paredes de la habitación. Este tipo de solado se denomina, por tanto, flotante. Además de las propiedades de aislamiento térmico, las soleras flotantes aumentan las cualidades de aislamiento acústico. . Esto juega un papel importante cuando se utilizan este tipo de revestimientos en los pisos superiores de la casa.
Si no hay forjado en la planta baja de la casa, se coloca un suelo denominado SO en el suelo. El suelo de la planta baja es una base negra y cálida sobre la que se instala la solera de hormigón. Para ello, se lija la base de la habitación, se compacta, se alinea, se cubre con una capa aislante y se vierte hormigón o mortero de cemento. El grosor de la solera subyacente debe ser de al menos 3 cm. Tras la solidificación, la base acabada imitará un solapamiento de hormigón.
Si la casa no puede soportar cargas pesadas, se puede prestar atención a las soleras secas, que son una alternativa a las bases tradicionales, pero tienen tanto ventajas como desventajas en comparación con el cemento moi
Herramientas y materiales
Se necesitan los siguientes materiales
- Cemento. Adecuado para habitaciones con mucha humedad. Existe riesgo de agrietamiento debido a la elevada retracción de este material.
- Yeso. Las soleras realizadas a base de yeso son muy plásticas y fáciles de peinar. No sufre contracción y se seca rápidamente. Es la base ideal para rellenar suelos cálidos.
- Mezclas autonivelantes. En poco tiempo se obtienen superficies planas con un grosor de 3-30 mm. El material se crea para formar un revestimiento de acabado.
Es necesario disponer de las siguientes herramientas
- Un recipiente para amasar la solución; y una gran superficie — una hormigonera.
- Nivel (mejor láser);.
- Reglas;.
- Espátulas de diferentes longitudes y formas.
- Taladro con boquilla mezcladora.
- Materiales auxiliares (cuerda, tiza o lápiz, metro).
Cálculo del número de materiales necesarios para el enrasado.
En el paso anterior se ha determinado que el espesor medio de la solera en el ejemplo condicional es de 30 mm.
Para el cálculo se necesita la superficie de la habitación; suponemos que es de 20 m2 .
También es necesario determinar la marca del mortero de cemento y arena que se va a utilizar. Para ello, puede dirigirse de nuevo a la sección nº 8 SP 29. 13330. 20011 «Caídas». A partir de la información de esta sección, se ha elaborado la siguiente tabla
Tabla 1 — Dependencia de la marca de la solución en función de la finalidad de la solera
Hemos acordado que estamos considerando una solera clásica de cemento y arena de nivelación a base de hormigón. Por lo tanto, hemos elegido una solera adecuada para nosotros, que hemos decidido utilizar para el objetivo de nuestro proyecto de solado.
Ahora tenemos todos los datos para empezar a calcular los componentes necesarios de la solución.
Los cálculos pueden realizarse de varias formas: para mezclas acabadas (compradas) y para preparaciones independientes.
1) Cálculo del CPS acabado
Si se utiliza un CPS acabado, su consumo se indica en el envase. Normalmente es de 17-20 kg/m2 con un espesor de capa de 10 mm.
Ejemplo de CPS acabado (el consumo de la mezcla se indica en el envase)
Por lo tanto, la cantidad necesaria de mezcla puede calcularse según la siguiente fórmula
МMezcla= r x s x (t/10)
R — consumo de mezcla, kg/m2
S — superficie de la sala, m2
T — espesor de la solera, mm (en el ejemplo — 30 mm)
Aceptar el consumo a lo largo del límite superior, es decir, 20 kg/ m2.
МMezcla= 20 x 20 x (30/10) = 1200 kg (24 sacos de embalaje de 50 kg)
Las ventajas de utilizar CPS acabados son el ahorro de tiempo de cocción y las proporciones exactas de los componentes.
Las desventajas son los costes más elevados en comparación con la compra de cemento y arena, frente a la menor calidad del CPS. Además, la baja calidad de los fabricantes sin escrúpulos que ahorran dinero, aumentan la proporción de arena en la mezcla y utilizan cemento de baja marca.
Por lo tanto, hay que tomarse en serio la elección del CPS acabado y simular las opiniones de los clientes.
2) Cálculo de componentes en la autopreparación.
Paso 1. Calcule primero el volumen de la solera de cemento y arena. Para ello, multiplique la superficie de la habitación por el grosor medio de la solera.
VSolado.= S * t = 20 * 0,03 = 0,6 metros cúbicos
Paso 2: Determinar las proporciones de los componentes.
En la elección de la composición del mortero y del hormigón intervienen laboratorios especializados.
Esto se debe a que sólo realizando un estudio de los componentes que forman el hormigón o mortero se pueden determinar con precisión las proporciones para obtener las propiedades requeridas del material.
En el hogar, se puede utilizar una proporción universal de cemento y arena (1:3 en volumen), muy adecuada para las necesidades domésticas.
También puede comprobarlo usted mismo consultando la norma SP 82-101-98 «Preparación y uso de morteros de construcción», es decir, la tabla nº 4 (véase más abajo). Aquí vemos que se necesitan 350 kg de cemento M400 por metro cúbico de arena para preparar la solución M150. Si la densidad del cemento es de 1200 kg/m3 , esto corresponde a una relación de casi 1:3.
Tabla nº 4 Fragmento de SP 82-101-98 «Preparación y utilización de morteros de construcción
Paso 3. Determinar la cantidad de cemento. La tabla anterior muestra también el consumo de ligante, es decir, el consumo directo de cemento por m3 de solución. Es decir, es de 400 kg.
Entonces, para preparar los 0,6 m3 de solución necesarios, se necesitan aproximadamente 400 * 0,6 = 240 kg de cemento.
Paso 4: Determinar la cantidad de arena. El consumo de arena se determina por volumen en la proporción 1:3 (no se conoce el peso específico). Para ello, se divide el volumen calculado de la solución (0. 6 m3) por el número de partes proporcionales (es decir, 4) y se multiplica por el número de partes de arena (es decir, 3).
VArena= 0. 6:4*3 ≈ 0. 5 m3 (750 — 850 kg en función del tamaño de la arena, la humedad y la densidad aparente)
Debido a la relación de volumen 1:3 de los componentes, es conveniente mezclar la solución utilizando un recipiente de medición de uso general. Por ejemplo, vierta 3 cubos de arena y 1 cubo de cemento o 6 cubos de arena y 2 de cemento en una hormigonera. También es útil utilizar una pala para contar los ingredientes que se van a mezclar.
Fecha de actualización: 11-20-2023
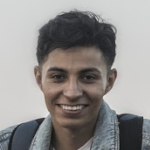
Este tema está cerrado para la publicación de respuestas.