Por supuesto, la finalidad de la habitación también influye en el grosor de la solera. Para guarderías, por ejemplo, hay suficientes indicadores estándar. Si se trata de un garaje, donde la superficie experimenta cargas más intensas, el grosor de la capa debe aumentarse. Los expertos también recomiendan colocar una capa de refuerzo adicional. Esto aumentará significativamente la resistencia de la superficie del suelo.
Tenga en cuenta que, bajo las baldosas, la capa de solado debe calcularse de modo que la superficie de las baldosas se caliente. De lo contrario, no se puede lograr el impacto requerido en el calentamiento de la habitación.
Bueno, hablando de cómo la capa máxima debe cubrir el suelo de agua, esto depende totalmente de la habitación — por ejemplo, si se trata de un almacén, aquí la regla puede llegar a 20 cm.
Tabla
- Espesor de la solera caliente
- Espesor necesario de la solera bajo el agua
- 4 Factores de la solera en suelos calientes que proporcionan calidad de base
- Material de sondeo.
- Al verter el solado de hormigón, exprima el trabajo
- ¿Qué tipos de solado son adecuados para suelos calientes?
- Acabado.
- Colocación de un suelo caliente sobre losas de poliestireno.
Espesor de la solera caliente
Al instalar un suelo caliente, hay que tener en cuenta que en los sistemas con calefacción por agua, la solera de hormigón es un material que distribuye el calor. Teniendo esto en cuenta, para conseguir resultados cualitativos, se debe utilizar una mezcla autonivelante con propiedades de curado acelerado (que se vende envasada) o una solución normal de cemento y arena.
El espesor mínimo admisible de la solera de lecho caliente de agua es de 30 mm por encima de la superficie de la tubería. En caso necesario, se permiten espesores de 150 mm o más, en cuyo caso deberán elaborarse cálculos especiales para el modo térmico de la zona calentada y tenerse en cuenta factores de corrección específicos. No obstante, para indicaciones óptimas, se toma un grosor de 7-10 centímetros. En cuanto a los suelos eléctricos, la norma aquí es de 3-5 centímetros.
Al hablar de solados, también es importante tener en cuenta el tiempo de curado y secado de la superficie. En condiciones normales, esto se determina en función del material utilizado, el grosor de la solera e inevitablemente tiene en cuenta el tipo de pavimento
En el caso del mortero de cemento y arena para parquet, este plazo debe ser de al menos 25-30 días. Dichos plazos se suman a partir de los siguientes cálculos. 1 semana por cada centímetro de solado hasta 4 cm y de 1,5 a 2 semanas por cada uno de los centímetros siguientes.
Las baldosas cerámicas pueden colocarse sobre una base de arena de cemento transcurridos aproximadamente 7-10 días. Quemar y alinear la mezcla apenas cuesta; de 1 día a 3-4 semanas. Todo depende del tipo de aditivo polimérico utilizado en la fabricación de la composición. Por lo tanto, a la hora de seleccionar el material adecuado, hay que tener en cuenta no sólo el posible grosor de la solera, sino también el tiempo que hay que esperar antes de colocar el revestimiento de acabado.
Espesor necesario de la solera bajo el agua
Al planificar el esquema de solado cuando se instala calefacción por agua bajo el suelo, es importante conocer el grosor de la solución que se va a rellenar. Al fin y al cabo, de ello depende la eficacia del sistema y su vida útil
Utilizar una capa fina ahorra combustible. Los «puff pies» (revestimiento de napol) tienen una transferencia de calor muy alta, pero la calefacción se desprenderá. No se puede utilizar. La capa gruesa capta la mayor parte del calor y reduce considerablemente el rendimiento de la caldera. Esto se traduce en unos costes de combustible muy elevados.
Si alguien piensa que el grosor óptimo de la solera para un suelo caliente está impreso en todas las tablas o instrucciones, está muy equivocado. Son varios los factores que determinan los parámetros del tamaño de la solera, para los que simplemente no existe una respuesta específica. Entre ellos
- Tipo de base del suelo: solapado de hormigón, suelo negro de madera, suelo individual de la casa.
- Los requisitos de régimen de temperatura de la habitación climatizada.
- Altura del techo;.
- Presencia de una pendiente a los pies del suelo.
- Espesor de las tuberías colocadas.
- Tipo de solución utilizada;.
- Configuración de la instalación.
- Función de la solera.
Basándose en los requisitos enumerados, los expertos distinguen tres tipos de soleras en función de su grosor
- Mínimo — unos 2 cm de grosor vertido con un compuesto autonivelante sin refuerzo.
- Óptimo (medio) — grosor de 5-7 cm; y
- Máximo: hasta 17 cm.
Considere con más detalle qué tipo de solado se vierte.
Mínimo.
Según Snip, el espesor mínimo posible de verter tuberías de calefacción de agua:
- 20 mm para mezclas con capas autonivelantes.
- 30 mm con una rejilla de refuerzo debajo de la tubería.
- 40 mm para solución de hormigón sin elementos de refuerzo.
El espesor de la solera de 20 mm sólo puede obtenerse con una opción. Tubería de calefacción de 16 mm de diámetro, uso de mezcla rápida ya preparada, tubería oculta y relleno de la solera con baldosas en el suelo. La exclusión de cualquier combinación de elementos provocará una rápida destrucción tanto de la solera como del suelo.
Espesor mínimo de la solera.
Cuando se utilizan soluciones de cemento, no todo es tan sencillo. Una capa mínima de solado (4 cm) sólo puede obtenerse con una superficie perfectamente plana de la base del suelo y un diámetro mínimo del tubo. Las variaciones de altura suman varios centímetros. Un aumento de la sección de intersección de los tubos también contribuye a aumentar el grosor del relleno. Por ejemplo, si la base del suelo tiene una pendiente de 1 cm y los tubos un diámetro de 25 mm, el espesor de la solera será de 7-8 cm.
Si la mitad de la solera de humos se coloca sobre un suelo calentado, el espesor mínimo será de 5 cm, con una solera negra y un diámetro de tubería de 16 mm.
Máx.
En cuanto a indicadores como el grosor máximo de la solera, Snip no dice nada: simplemente no hay datos. En la práctica, sólo se basan en dos casos
- La base de la solera está fuertemente iluminada.
- La solera cumple la función de cimiento (principio básico de la construcción de casas individuales en Alemania).
En el primer caso, es mejor nivelar primero la base del suelo y después instalar y rellenar los tubos de calefacción, con lo que la habitación se calentará más eficazmente; en el segundo caso, el relleno de la solera con agua caliente no debe superar los 17 cm. Rellenar capas gruesas no tiene sentido. En Rusia, las soleras más grandes se vierten en garajes y suelos problemáticos durante la construcción de casas particulares.
Óptimo.
El relleno medio (óptimo) de la solera es de 45-70 mm. Fibra — Con el uso de fibra (puede leer sobre este tema en el artículo «Fibra — solado de fibra») se obtiene un revestimiento resistente del tubo que soporta cargas dinámicas y estáticas considerables. En estos casos, la altura de la solera sobre el agua sólo puede ser de 25-30 mm por encima del suelo caliente. Si se utilizan mallas o varillas de refuerzo, el grosor total de la solera no debe superar los 6-7 cm.
4 Factores de la solera en suelos calientes que proporcionan calidad de base
La tecnología moderna, incluida la construcción, tiene tales matices que su tarea consiste en garantizar la calidad específica de lo que se fabrica: una sutileza fundamental, por así decirlo. Violarlas significa actuar por cuenta propia. En este sentido, las soleras con calefacción y las soleras eléctricas no son suficientes en un contexto general. Hasta el momento básico de garantizar la durabilidad, se pueden atribuir cuatro cosas
- Aislamiento térmico eficaz: impide que la máxima cantidad de energía térmica contenida en la habitación se propague al forjado. Esto se consigue mediante el uso de dos tipos de materiales de aislamiento térmico. No permite que el hormigón frío del forjado enfríe rápidamente los elementos calefactores y, de hecho, permite que el aislamiento térmico refleje Dirige el flujo de energía térmica hacia la habitación. El material se coloca en capas: primero el encofrado (su grosor no debe ser inferior a 30 mm) y después se extiende sobre él el aislamiento térmico reflectante, con cinta de aluminio pegada entre medias.
- Refuerzo de alta calidad. Gracias al refuerzo metálico de la solera, ésta no se destruye bajo la influencia de las cargas. No hay que subestimar la importancia de este elemento de la solera, ya que debajo de ella hay un material blando que puede deformarse fácilmente, con lo que la solera desatendida simplemente se agrietaría.
- Cinta amortiguadora. Su tarea consiste en resistir la deformación por temperatura de la solera. No hay material que no reaccione a la temperatura en su dilatación. Las soleras que no están firmemente satisfechas con la losa del suelo, alargándose en todas direcciones, empiezan a levantarse en forma de torta sobre la pared. Como resultado, aparecen todas las mismas grietas. La solera agrietada no puede distribuir la carga uniformemente y debido a estas deformaciones pueden dañarse los elementos calefactores del suelo caliente. Esto se soluciona con cinta amortiguadora, un material blando y poroso. Como alternativa, una espuma de baja densidad colocada a lo largo de todo el límite de la habitación junto a las paredes puede actuar como amortiguador.
- Es difícil sobrestimar el papel que desempeñan las mezclas de solado y otras mezclas para suelos calientes en la creación de solados bajo el agua. Una solución adecuadamente preparada en la que se observan claramente las proporciones de todos los componentes necesarios — esta es la clave para la calidad de la planta, es decir, su resistencia y capacidad de soportar cargas, sino también su conductividad térmica. Una solera de este tipo en un suelo de cemento no es inferior a 300 marcas, fracción de 0,9 mm, arena con fibras (fibras de polipropileno destinadas a aumentar la resistencia de la solera) y agua. Todo ello se mezcla en la proporción de 1 parte de cemento, 3 partes de arena, 0,7 partes de agua y 1 decímetro cúbico de fibras. También se pueden añadir a la solución plastificantes y modificadores especiales. Esto permite reducir el grosor de la capa de solado en el suelo, y los segundos confieren a la solución propiedades adicionales (por ejemplo, no se congela a temperaturas negativas).
Sobre todo, un matiz importante es el grosor de la solera del suelo radiante. No debe ser inferior a 50 mm de la capa de aislamiento térmico. Si se vierte, se corre el riesgo de que aparezcan grietas después de la primera temporada de funcionamiento.
Cuál es el grosor de la solera caliente
Material de sondeo.
Una vez colocadas las tuberías, comienza la siguiente fase: el solado. Suelos calientes se llevan a cabo por medio de dos tipos de solado
- Hormigón — preparado de forma independiente a base de cemento.
- Semi-absorbente — se utiliza la mezcla acabada.
Solera de hormigón.
En las instalaciones de suelos calientes se suele utilizar mortero de cemento y arena o relleno de hormigón. Para que la solera sea de alta calidad y dure muchos años, hay que respetar una serie de reglas.
- La solución se prepara a partir de tres componentes: arena, agua y cemento. La marca del cemento utilizado no debe ser inferior a M300, algunos hasta 5 mm. Para una mejor adherencia, se recomienda ingerir arena, pero su cribado.
- El solado se realiza sobre un suelo caliente y conviene añadir un plastificante a la solución para aumentar sus propiedades físicas (resistencia). Gracias a este aditivo, el solado en suelos cálidos durará más tiempo porque adquiere plasticidad y resistencia adicionales. El plastificante se añade en una proporción calculada entre 0,6 y 1 litro por metro cuadrado.
- Si el grosor de la solera es inferior a 30 mm, es obligatorio añadir plastificante; a partir de 50 mm, no se puede añadir plastificante.
- Si se proyectan soleras finas de hormigón para habitaciones grandes de 40 m2 o más, es muy importante que se añadan fibras a la solución, además de plastificantes. Actúan como una malla reforzada, rellenando la solera uniformemente y reforzándola.
Además de una solución bien preparada, la solera inundada debe secarse adecuadamente una vez que se haya dispersado en una capa uniforme por toda la superficie del suelo. No se pueden utilizar dispositivos auxiliares para el secado. Sobre todo en suelos calientes. El curado del hormigón debe producirse de forma natural. Dos días después de rellenar el suelo, hay que humedecerlo, verter agua y cubrirlo con un hule. El fraguado completo del hormigón se produce en 28 días. Durante este tiempo, la solera se fortifica al máximo e, idealmente, el suelo debe permanecer cubierto con hule durante este tiempo. mojado cada 3 días. Esta técnica evita que la solera se agriete.
Mezcla a medio fumar
Durante la venta, ya hay preparada una mezcla especial para verter la solera en agua caliente. Para cocerla, basta con añadir una pequeña cantidad de agua, respetando las proporciones indicadas en el envase por el fabricante. La mayoría de los expertos prefieren una mezcla semiseca. Y todo:
- En comparación con el mortero de cemento y arena, las mezclas semisecas tienen mayor resistencia.
- No es necesario esperar 28 días para que el suelo se endurezca por completo. Este tipo de solado se seca más rápido, lo que le permite terminar rápidamente las reparaciones de la habitación.
Para que un solado de mezcla semiseca funcione durante mucho tiempo, debe elegirse correctamente. Es preferible utilizar productos que contengan modificadores. Rellene siempre la capa de refuerzo.
Al verter el solado de hormigón, exprima el trabajo
La solera bajo el suelo radiante se vierte una vez colocadas las capas de impermeabilización, aislamiento y acuífero. Refuerce con malla metálica de al menos 3 mm de diámetro de varilla. Las tuberías suelen fijarse al refuerzo y bajo el sistema de suelo caliente. Sin embargo, muchos expertos consideran que la posición de la armadura por encima de la tubería con agua es adecuada para la correcta distribución de la carga mecánica por toda la superficie de la solera. La colocación de esta armadura también contribuye a la salida óptima de la energía térmica del espesor del hormigón.
La capa de impermeabilización se ejecuta según una solera negra con impermeabilización en rollo o revestimiento líquido.
A continuación, se instala una capa de aislamiento. Por regla general, se utiliza poliestireno de alta densidad (35 kg/m3 o más). Las placas de poliestireno se fabrican con dispositivos de bloqueo en los bordes para que puedan colocarse de la forma más compacta posible.
La composición de la mezcla de cemento debe cumplir las normas del hormigón y contener el grado adecuado de cemento, arena o piedra triturada y plastificantes. Para aumentar la resistencia de la solera calefactada, se recomienda añadir fibra a la solución. Se trata de un tipo adicional de refuerzo consistente en material de fibra sintética.
El solado bajo los suelos con calefacción debe realizarse al mismo tiempo. No es posible inundar una zona durante una pausa de varios días. Esto podría provocar grietas durante las operaciones posteriores. Cuando se vierte una gran cantidad de solado bajo un suelo radiante, se puede dividir la producción en fases específicas. Por ejemplo, verterla habitación por habitación, restringiendo la zona de solado al umbral de la puerta, tras lo cual se instala debajo una junta de compensación térmica.
Las tuberías de agua deben estar en perfecto estado de funcionamiento antes del vertido, ya que quedan inaccesibles una vez fraguado el hormigón. A este respecto, se prueban los sistemas de calefacción por suelo radiante. La presión del agua de trabajo se conecta a las tuberías y se comprueba si hay fugas a lo largo del día. Si se produce una fuga, debe eliminarse y sólo entonces puede verterse la solera de hormigón.
Cumplimiento de las normas
Un aspecto importante es el cumplimiento de las normas para la instalación de soleras en suelos calentados por agua relativas al proceso de dilatación térmica.
A lo largo del perímetro de la habitación, en la unión entre la solera y la pared y en las puertas, deben colocarse listones de borde de al menos 5 mm de grosor. Se fijan a la pared con grapas y grapas metálicas. Si la pared es de hormigón y no se pueden fijar grapas metálicas, la cinta de borde se puede fijar a la pared con adhesivo.
Una vez fraguada la mezcla de cemento, el exceso de cinta de borde de espuma de polietileno puede recortarse con una espátula afilada hasta el nivel de la capa de acabado.
La segunda condición, que a menudo se ignora, es la instalación de un interruptor de deformación por cada 8 metros lineales de solado vertido sobre el suelo calentado por agua. Sólo la presencia de un rompedor de deformaciones garantiza la protección del suelo contra las grietas causadas por la dilatación y contracción térmicas.
La profundidad del hueco de compensación debe coincidir con la distancia hasta la parte superior del revestimiento de acabado, siendo la profundidad de la solera igual a la distancia entre las capas de impermeabilización. Anchura: al menos 10 mm.
Si la superficie de la solera está revestida con baldosas cerámicas, la junta de deformación debe transmitirse a las baldosas. Para dar un aspecto estético del borde con molduras de metal o plástico. En el interior de la ranura se vierte un sellador elástico acrílico o de silicona. Gracias a ello, el polvo, la suciedad o el agua no se acumulan en las juntas.
Si el suelo acabado es un suelo flotante (parquet), moqueta o linóleo, la junta de deformación queda oculta bajo la superficie exterior. Para evitar que se astillen, los bordes de las juntas se refuerzan con esquinas galvanizadas pintadas.
El secado completo de la solera dura entre 28 y 30 días desde el momento del llenado.
¿Qué tipos de solado son adecuados para suelos calientes?
Para crear la base del suelo, se vierte un mortero de cemento — solado — en las tuberías de calefacción. Esto último ocurre:
Suelos cálidos.
Para el tipo de solado húmedo, se vierte una solución de cemento con arena añadida. Esta es la forma más fácil y sencilla de cerrar las tuberías de calefacción, ya que no requiere conocimientos específicos por parte de los contratistas ni equipos especiales. La solución puede amasarse en un recipiente grande equipado con un perforador sin recurrir a una hormigonera.
Para mayor prosperidad económica, se puede comprar una solución seca en la que ya se han observado las proporciones entre aditivos, arena y cemento, en lugar de los componentes de la mezcla. Basta con verter agua y remover. Otra ventaja de este tipo de solado es que es el más fino y, por tanto, el que menos espacio ocupa.
La composición de los componentes sólidos de una solera semilenta es similar a la de una solera húmeda (cemento, arena de cantera, fibras y plastificantes). La diferencia en la cantidad de agua es de sólo 1/3 del volumen de la mezcla.
Es muy difícil colocar uno mismo un solado semiseco. Siempre se necesita una hormigonera (es difícil remover manualmente o incluso imposible) y una plancha vibratoria. Alquilar el equipo puede resolver el problema, pero sin experiencia trabajando con vibradores puede estropear el trabajo realizado.
La mezcla debe ser comprado en forma acabada — es difícil adivinar la cantidad de plastificante.
Conclusión: si usted planea hacer el trabajo con sus propias manos, es mejor rechazar la mitad de la regla.
El solado seco está hecho de material a granel (arcilla expandida). Una vez acondicionado el relleno, se coloca madera contrachapada, tejas acondicionadas con yeso o aglomerado bajo el pavimento de acabado. Todos los materiales son asequibles. Se pueden encontrar en cualquier gran tienda de construcción. Una tecnología sencilla permite realizar el trabajo uno mismo.
Este método de solado tiene dos inconvenientes importantes
- La capa gruesa de solado alcanza los 8-12 cm. Por lo tanto, no se recomienda rellenar la calefacción con arcilla expandida en habitaciones con techos bajos.
- La conductividad del calor de la tubería al suelo.
Las ventajas e inconvenientes de cada tipo de solado se explican detalladamente en la pieza.
Acabado.
La colocación de la solera caliente tiene lugar una vez finalizados todos los trabajos de preparación e instalación. En la producción de construcción moderna, el revestimiento acabado del suelo de agua consta de aislamiento, impermeabilización, elementos calefactores, solado y revestimiento de acabado.
- Preparación. Se limpia la superficie para rellenarla de la entrada de solución y polvo. A continuación, se impregna la base de hormigón con masilla bituminosa y se aplica con un rodillo de pintura de 250 mm.
- Refuerzo. Sobre la superficie preparada se coloca una pila metálica con celdas de 50-100 mm. Entre ellas, las chapas se fijan con alambre trenzado.
- Colocación del aislamiento. Lana mineral basáltica y espuma extruida. El grosor de la capa es de 50-100 m. Para 100 mm, se colocan dos filas de 50 mm de aislamiento cada una.
- Cinta amortiguadora. Se pega en todo el perímetro de la habitación, entre la pared y el suelo. La cinta nivela la dilatación térmica de la solera final.
- Instalación de elementos calefactores. Cuando se utilizan planchas de espuma normales para el aislamiento, se hacen zanjas en ellas en las que se colocan las tuberías. Existe una estera ondulada en la que la disposición de las tuberías ya está preparada y acabada con placas de aluminio que reflejan el calor.
Existe una tercera opción. El suelo radiante se instala a partir de bloques prefabricados que se recogen en el lugar. El líquido especial para la calefacción ya está inundado en las tuberías.
¡Importante! Después de verter el hormigón es difícil determinar dónde funcionarán las tuberías. Por lo tanto, dibuje un mapa de la ubicación de los elementos de calefacción.
Esto aliviará los problemas a la hora de excavar el suelo en el futuro.
- Instalación de faros, utilizando perfiles metálicos con nervaduras de 10 mm y pasos de 600-100 mm. Montados sobre montículo de mortero.
Los faros se colocan a lo largo de las paredes de la habitación. El primer perfil se coloca a 300-400 mm de la pared. Se utiliza un nivel láser para determinar el horizonte. El primer faro se fija a él. Para el resto, las marcas se transfieren utilizando niveles de construcción de 1000-1500 mm de longitud. Comienzan a rellenarse 24 horas después de la instalación de los faros.
Importante La distancia entre dos faros adyacentes debe ser inferior a la longitud de la regla. De lo contrario, la regla no podrá alinearse cualitativamente.
- Vertido. Las soleras de acabado para lechos de agua se preparan a partir de hormigón, arena de cemento o tienda. En la mayoría de los casos, la mezcla se amasa directamente en la obra. A continuación se indican las proporciones de los componentes.
La solera de hormigón para suelos calientes se vierte con franjas que comienzan en las esquinas más alejadas. Su grosor depende del tamaño de las tuberías y de cómo estén colocadas. El valor medio para los lechos de agua es de 50-70 mm. Las superficies con reglas se nivelan con un movimiento ondulatorio.
Durante el proceso de llenado pueden producirse pausas. Este espaciado no influye suficientemente en el revestimiento monolítico. Hay formas de minimizar la pérdida de resistencia por un relleno irregular. Antes de continuar con la colocación de la solución, las zonas extremas se humedecen de agua y cemento por la familia.
El plazo de secado de la solera depende del grosor de la estancia y de la humedad general. Por término medio, hay que dejar pasar de 10 a 14 días. Si la habitación es demasiado calurosa, se puede regar la solera con agua cada 12 horas durante una semana.
Hay formas de diluir con precisión la preparación de la superficie. Se coloca una servilleta de papel sobre el hormigón y se cubre con una jarra encima; al cabo de 12 horas se retiran las orillas. Si la servilleta permanece seca, la solución se ha secado, si está húmeda, aún no ha curado hasta el final.
¡Importante! En el sistema, el grosor del suelo caliente a base de hormigón o arena de cemento afecta a las propiedades térmicas; si 30-40 mm es demasiado fino, la calidad de la calefacción se deteriorará.
- Juntas de deformación. Son necesarias en habitaciones con una superficie superior a 20 m2 . Las costuras se cortan en pasos de 1500-2000 mm. Para ello, utilice una amoladora y un círculo de sierra en el hormigón. La anchura de las costuras es de 2-3 mm. Después de beber, se limpian de polvo y se sellan con sellador a una profundidad de hasta 2/3. Las costuras restantes se cubren con mortero de cemento y arena. Las costuras deformadas cualitativamente evitan la aparición de grietas en la solera debido a las fluctuaciones de temperatura.
Colocación de un suelo caliente sobre losas de poliestireno.
Una opción para sustituir las soleras son las placas de poliestireno. Se fabrican en forma de esteras de 30 mm de grosor, 0,3 m de ancho y 1,0 m de largo con salientes en forma de resaltes o ranuras, entre los que se colocan las tuberías.
Para instalar los tubos en las esteras de poliestireno, es necesario realizar las siguientes operaciones
- Comprobar el grado de diferencia de altura en la base del suelo. El indicador no debe superar los 2 mm por cada 2 m2. Si se supera este valor, se debe crear una solera de hasta 1 cm de grosor utilizando una mezcla autonivelante.
- Limpiar la superficie del subsuelo de escombros y polvo.
- Realizar la impermeabilización — se coloca una lámina de polietileno de 0,2 mm de grosor sobre el subsuelo y se superpone a la pared. Las juntas de conexión se sellan con cinta de construcción.
- La cinta amortiguadora se fija alrededor de la pared utilizando una grapadora de construcción o adhesivo — compensa la expansión de la solera bajo la influencia de los cambios de temperatura y humedad.
- Colocar la solera cerca de la pared.
- Fijar las losas con adhesivo.
- Marcado de tuberías. En este caso, hay que seguir algunas reglas. Para dos habitaciones contiguas, independientemente de su superficie, debe haber contornos independientes; la superficie máxima que puede cubrir un circuito es de 40 m2. La anchura entre tuberías paralelas debe ser de 20-30 cm.
- Coloque los tubos entre los resaltes según el esquema preparado.
Coloque los tubos encima de la placa de poliestireno.
Nota: Cuando se utiliza poliestireno sin resaltes, algunos artesanos colocan una placa metálica debajo de los tubos. Esta es una opción si «no puedes estropear tus gachas con mantequilla».
- Comprueba la estanqueidad de las conexiones de las tuberías durante el día y las propiedades térmicas del suelo.
- Coloca una película de espuma de poliestireno o polietileno sobre las tuberías. Para mejorar la estanqueidad, la película se extiende sobre la pared en capas superpuestas. Las juntas se pegan con cinta adhesiva.
- Se superponen dos capas de cartón-yeso de 10 mm de grosor; las juntas de la segunda capa no deben coincidir con las juntas de conexión de la primera. Las láminas de tablero de fibra de yeso se fijan con tornillos de rosca y no se debe dañar la lámina que las recubre.
- Enmasillar la junta bajo el linóleo y el laminado (esta operación no se realiza bajo las baldosas).
Fecha de actualización: 11-20-2023
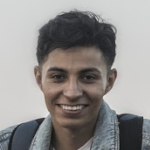
Este tema está cerrado para la publicación de respuestas.