Si las propiedades del suelo lo permiten, sólo se puede construir la base de bloques FBS.
Sin embargo, las denominadas bases monolíticas prefabricadas son las más extendidas. La diferencia fundamental entre una base de este tipo y las cimentaciones monolíticas convencionales es que sólo se debe hormigonar cuando se colocan los blindajes superior e inferior. Damos unas sencillas instrucciones paso a paso para la fabricación de cimentaciones de bloque — justificación.
- En primer lugar, marque y excave una zanja (por analogía con una cimentación en bandas estándar).
- En el fondo de la zanja, vierta una capa de arena (de 10°C de espesor) y recórtela completamente con planchas vibratorias.
- A continuación, se vierte una capa igual de piedra triturada y se compacta con cuidado.
Nota. En suelos arcillosos, se utilizan como suelo espacial bandas recubiertas de SO (mezcla de arena, grava y cemento) que, en contacto directo con el agua, son más resistentes que el suelo circundante y protegen la parte inferior de la base.
- El soporte inferior blindado está equipado con un encofrado bajo.
- Lo rellenamos con polietileno denso (para evitar la rápida eliminación de la humedad).
- Colocamos dos capas de armaduras (la inferior trabaja, la superior — estructura).
- Verter solución concreta.
- Una vez alcanzado el 20% de la resistencia de la «Vykatonka» (esto es aproximadamente un día después de verter la solución), proceder a la instalación de los bloques FBS utilizando una grúa de elevación. La mampostería se inicia en el ángulo de la base (la tecnología es similar a la de los ladrillos) y se produce en una solución de cemento y arena. Esto debe rellenar las cavidades verticales entre los productos; la segunda y subsiguiente capa se crea «arraigando» en el bloqueo de los bloques.
¡Importante! La correcta instalación de cada unidad se controla (vertical y horizontalmente) utilizando niveles (vertical y horizontal)
- Después de colocar el producto, equipamos el soporte superior blindado con encofrado.
- Los marcos de refuerzo se colocan en el interior y todo se vierte con soluciones de hormigón.
Más información La cinta de refuerzo superior cumple varias funciones básicas Se ajusta a las irregularidades que puedan producirse al instalar los bloques. Distribuye la carga uniformemente por la cinta de cimentación y aumenta la resistencia general de la base.
- Extiende parcialmente la costura exterior del jadeo y la rellena con una mezcla especial (adición impermeabilizante).
- Realizamos todos los trabajos necesarios de impermeabilizacion de los cimientos.
Y sólo después rellenamos la zanja.
Tabla
- Tipos de bloques.
- ¿Qué es una prensa vibratoria?
- Tecnología de producción de bloques de silicato de gas
- Descripción de la tecnología de producción.
- Cómo crear bloques de hormigón de escoria
- Bloques caseros
- Preparación de la solución para los bloques
- Equipo
- Se recomienda utilizar máquinas para bloquear
- Equipamiento industrial
- Tipos de productos de hormigón
Cómo construir bloques de cimentación con sus propias manos
Para hacer el encofrado, es necesario obtener una hoja de madera contrachapada OSB. Su anchura es igual a la altura del bloque y su longitud es 20 cm mayor que su longitud. Un lado de la madera contrachapada se limpia y se pinta con pintura resistente al agua.
Una vez seca la cara pintada de ambos tableros, se realizan cortes transversales a una profundidad de unos 5 mm, con sierras de arco a 10 cm del borde.
La distancia entre ellos en cada contrachapado debe ser igual a la longitud del bloque. Ahora, entre cada contrachapado y corte, casi en el centro, se taladra un agujero de 14 mm de diámetro — para los futuros tornillos de la regla.
Las dos secciones rectangulares se cortan de chapa de acero de 1 mm de espesor. Un lado de cada uno es igual a la altura del bloque, el otro a la anchura.
Actúan como insertos finales en el encofrado y se han hecho goterones para ellos. También se pueden utilizar tableros contrachapados o acabados.
Preparando unas varillas de acero de 12 mm de diámetro y 10 cm más largas que la anchura del bloque, con roscas en los extremos se puede descansar y proceder al montaje.
Los tableros contrachapados se colocan sobre superficies planas paralelas entre sí por los lados pintados. Los extremos metálicos se insertan en los recortes y las varillas preparadas se introducen en los orificios redondos.
Antes de tirar de la estructura con tuercas, hay que colocar separadores de madera en el interior del contrachapado, junto a la regla, para fijar la anchura del bloque.
Ahora las tuercas están retrasadas y el encofrado está listo.
Para preparar la solución, hay que unir una parte de cemento con dos de arena y cuatro de grava. Para que los bloques sean resistentes, la mezcla debe seguir siendo muy viscosa después de mezclarla bien.
La consistencia deseada se consigue ajustando el suministro de agua. Antes de verter la solución en el interior de las paredes extremas, se pueden colocar barras de madera en el centro. Después se pueden retirar y dejar las ranuras. De este modo se garantiza que la solución esté llena cuando se coloquen los bloques listos.
Así se refuerza la unión entre ambos y se fortalecen los cimientos. A continuación se rellenan los encofrados con la mezcla y se compactan. Para evitar grietas durante el secado, se cubre la estructura con film y se riega regularmente durante dos días, tras los cuales se puede desmontar el encofrado.
Vídeo: Encofrado de bricolaje
Tipos de bloques.
- Bloques de hormigón: la escoria se utiliza como relleno de los bloques. Estos bloques son resistentes al fuego y a las bajas temperaturas.
- El hormigón de serrín es fácil de instalar. Es muy fácil de usar y ligero.
- Los bloques de grava son pesados y difíciles de colocar.
- Los bloques de arcilla espumada tienen excelentes propiedades aislantes. Son ligeros, pero resistentes.
- Bloques que contienen serrín, piedras y diversos materiales de desecho.
Para acelerar el proceso de producción, es necesario crear varios moldes. Para crear un bloque, es necesario
- Preparar los moldes para hacer los bloques
- Colocarlo sobre una superficie lisa y plana (de metal o de goma)
- Preparar una solución que contenga el relleno necesario
- Humedezca el molde con agua o aceite de máquina (para facilitar el desmoldeo)
- Aplicar la solución al molde preparado
- Para comprimir la solución y liberar el exceso de aire y agua, debe encenderse la plataforma vibratoria durante 2-4 minutos.
- La superficie del bloque debe aplanarse con una espátula
- Se puede utilizar una zona abierta con toldo para trasladar el molde a la zona de secado.
- Después de 30-40 minutos, retire el molde del bloque terminado.
- Deje el bloque en la zona de secado durante 2-3 días. A continuación, trasládelo a una zona seca durante 20-25 días. Tras este periodo, el bloque está listo para su uso.
Fabricación de bloques de cerámica
Los bloques de cerámica se fabrican con relleno de arcilla espumada.
Para crearla, se necesita lo siguiente
- 1 parte de cemento
- 5 partes de relleno de arcilla espumada
- Arena tamizada — 3 partes
- 1 parte de agua
La solución debe mezclarse para crear el bloque según las instrucciones siguientes.
- La solución se aplica a un molde engrasado
- Se comprime.
- Después de 15-20 minutos, se retira el molde
- Colocar el producto sobre una superficie plana; al cabo de 12-13 horas, trasladar a un lugar protegido de la lluvia.
- Al cabo de 20 días, los bloques están listos para la construcción.
Ventajas de este tipo de material de construcción:.
- Los bloques son ligeros
- Resistentes a las bajas temperaturas
- Resistentes a la humedad
- Gran resistencia
- Bajo coste
Fabricación de bloques de hormigón
El proceso de fabricación de bloques de hormigón puede dividirse en varias etapas sucesivas.
- Preparación de los moldes para la fabricación de bloques. Inicialmente, los moldes deben humedecerse con agua. De este modo, es imposible que se adhieran a las paredes interiores de la solución.
- Rellene el encofrado con la solución e instálelo en la plataforma vibratoria durante unos minutos para que la solución se contraiga.
- Una vez fijada la solución, se puede retirar el encofrado
El producto debe secarse sobre una base uniforme de caucho. De este modo se evitan daños en el bloque.
- Cemento — 1 parte
- Arena — 4 partes
- Grava superficial — 4 partes
- Cal — 4 partes
- Agua — hasta obtener la densidad media
Los bloques de hormigón adquieren resistencia después de 28 días.
Producción de bloques de hormigón opilacet
Antes de preparar los bloques, se necesitan los siguientes materiales
- Cemento.
- Una pequeña fracción de arena
- Cal
- Serrín
Para preparar la solución, se necesita
- Tamizar el serrín
- Mezclar cemento, arena y cal
- Añadir serrín y mezclar de nuevo
- Añadir agua hasta conseguir una densidad media
- Añadir cloruro cálcico para mejorar la adherencia
- La forma debe colocarse en vueltas
- Coloque la solución
- De cualquier forma conveniente
- Deje curar los encofrados durante 4-6 días
- Extienda el encofrado y déjelo secar otros 2 meses
Producción de bloques samany
Para la producción de bloques estructurales Kaman, es necesario
- Arcilla roja.
- Paja
- Arena de río.
- Agua.
No existen proporciones exactas. Las soluciones suelen evaluarse visualmente. Opción más óptima:
- Arcilla — 1 metro cúbico.
- Paja — 20 kg.
- Arena — 25-30%.
Para comprobar la preparación de la solución, tome un puñado de solución para formar una bola y dejar al sol durante 1-2 horas. A continuación, si la solución no se ha deshecho, tire la bola al suelo. Si se agrieta o se deshace, hay que reducir la proporción de agua y arena.
Para fabricar los bloques, hay que llevar a cabo las siguientes acciones
- Preparar una plataforma clara y uniforme
- Crear la solución
- Rellenar la forma con la solución
- Generar.
- Eliminar el exceso de solución con una espátula
- Después de 20-30 minutos, retirar el encofrado
Bloque seco 10-15 días. La condición principal es que no gane agua. Sea cual sea el método de fabricación de bloques, el coste de producción de este tipo de materiales de construcción es, en cualquier caso, inferior al de la compra de productos acabados. Los bloques autofabricados son mucho más respetuosos con el medio ambiente y existe la posibilidad de elegir los tamaños necesarios.
¿Qué es una prensa vibratoria?
A grandes rasgos, una Vibroprensa es una mesa potente, cuya encimera está suspendida por muelles u otro método. La vibración de la encimera se produce por el desplazamiento del centro de gravedad de una excéntrica unida al eje de salida de un motor eléctrico.
Hay varios tipos de suspensión de la placa vibratoria — suspensión de resorte, almohada de goma, pero el cable. Las camas fuertes deben apoyarse de forma estable y fiable en el suelo, mientras que la placa vibratoria comprime la mezcla de hormigón de escoria. En las máquinas fabricadas por métodos industriales, los equilibradores con centro de gravedad desplazado se instalan directamente sobre la placa vibratoria y se fijan rígidamente a ella. Las Vibr o-Strokes caseras utilizan diversos esquemas de accionamiento del equilibrador, pero esencialmente se trata de un accionamiento por correa y este diseño es fiable y de calidad para bloques de escoria.
Tecnología de producción de bloques de silicato de gas
Además del equipamiento, la producción requiere el conocimiento de las técnicas de producción y de las proporciones de las materias primas.
Proceso de producción de bloques de silicato gaseoso
Este proceso es muy fácil de poner en práctica. Si se aplican correctamente las proporciones y la tecnología, se obtiene un producto de alta calidad.
- La vibración se utiliza para separar el material a granel de los fragmentos no deseados.
- Moler la materia prima para la producción de bloques de silicato de gas en un molino de bolas.
- Respetar las proporciones y mezclar todos los componentes a granel excepto la suspensión de aluminio.
- Repetir el tamizado.
- Añadir el polvo de aluminio y el agua y mezclar bien.
- Llenar las formas con ½ de la mezcla total respectiva.
- Dejar la masa a una temperatura de al menos 40° durante 2 horas.
- Procesar el bloque en autoclave.
- Déjelo durante 3 horas para completar el proceso químico y el fraguado de resistencia.
Si desea fabricar bloques de hormigón estatal según las normas interestatales, familiarícese con las disposiciones de GOST 31360-2007, 21520-89, 25485-89 y 31359. .
Proporciones de los componentes para la producción de mezclas.
Considere qué bloque de tamaño de gas se está fabricando: para producir un metro cúbico de mezcla de capas de gas, se requieren las siguientes proporciones de ingredientes. Agua — unos 450 l.; cemento — 60 kg (8% a 10%); arena de cuarzo — 450 kg (hasta 70%); yeso — 0,5 kg (hasta 2%); cal — 120 kg (12% a 20% de cal); polvo de aluminio — 0,5 kg (hasta 2%).
Para alcanzar el índice máximo de densidad del material, la proporción de poros no debe superar el 38%. Tales unidades de construcción son adecuadas para la construcción de capital.
Setas de gas con un indicador de densidad media son materiales con una cuota de 52% o menos.
La porosidad máxima admisible de los materiales fotocelulares es de hasta el 92%. En este último caso, el uso de bloques de silicato de gas sólo está permitido para el aislamiento térmico.
Descripción de la tecnología de producción.
La producción de bloques de arcilla expandida afecta a las propiedades estructurales del material. Pueden ser monolíticos o huecos. Teniendo los materiales: cemento, arena, arcilla expandida en proporciones específicas — 1:2:3. los bloques se crean por etapas.
- En primer lugar, se realiza la combinación de todos los componentes.
- A continuación, se lleva a cabo el moldeado.
- A continuación, se bloquea y se cura el bloque.
- Por último, comienza el secado (al menos 2 días).
La densidad de los bloques depende de la proporción. La composición del hormigón de arcilla expandida puede ser inusual. Selección: en una parte de cemento deben ingerirse dos partes de arena seca, una parte de líquido y algunas partes de arcilla expandida. La mezcla creada puede resultar muy seca. Para evitar estos problemas, hay que sustituir el agua por una mezcla especial como el «hormigón de arena»; para curar los bloques se utiliza Vibropress. El proceso en sí dura aproximadamente dos días.
La producción de bloques de arcilla expandida también se lleva a cabo en los estados nacionales. Se pueden concluir diferencias no sólo en el proceso de creación, sino también en la composición de los materiales. Las proporciones de las estaciones de diseño creado individualmente de la siguiente manera:
- Grava — 8 partes;.
- Arena limpia — 2 partes;.
- Agua — 225 litros por m³ de mezcla creada.
También vale la pena destacar que puede ser necesario un poco más de arena. Esto se debe a que es necesario utilizar tres partes para crear la capa de material texturizado. Si se dedica a su propia fabricación, recuerde que necesitará utilizar detergente en polvo en el proceso de producción. Incluso una cucharada de polvo da plasticidad al producto acabado.
Moldeado.
Crear una solución normal: media caja. Moldear la mezcla es la siguiente fase de la producción. El moldeado se realiza utilizando la mitad de una superficie gruesa en forma de placa, cuyo grosor no debe superar los 20 mm. La tecnología de este proceso afecta a las dimensiones del bloque de arcilla expandida. Por término medio, el producto acabado pesa unos 16 kg y tiene unas dimensiones de 390 x 190 x 140 y 190 x 190 x 140 mm.
La elección de la calidad de los componentes también es importante a la hora de formar bloques de arcilla expandida
Listones de acero, aceite de máquina para lubricar las paredes que actúan como pestillos, tablones para las paletas del suelo… parece que cualquier cosa importa, pero todo ello afecta a la calidad del producto.
La mezcla debe ser normal (sin residuos ni arena de más). Hay que tener en cuenta varios «secretos» del proceso técnico. Con la ayuda de barras de madera, es fácil encofrar a lo loco
Al apisonar, observe el aspecto de la «leche» de cemento y haga coincidir la mezcla del suelo con la alineación de la llana.
Secado.
El secado es la etapa más importante en la producción de materiales de construcción; se asignan 2 días para los bloqueos de la unidad. Sin embargo, esto no es suficiente para las operaciones de construcción. El producto debe cubrirse con una película especial durante 20-30 días para evitar la rápida evaporación del agua. Sólo después de estas operaciones los bloques de arcilla expandida están listos para la venta. Gracias a las nuevas tecnologías, los tiempos de secado pueden reducirse ahora a 7 horas. Para ello se utilizan aditivos plastificantes. Se mezclan con la solución a razón de 5 g por producto.
Envasado y almacenamiento
Dado que los bloques de hormigón de arcilla expandida son resistentes a la humedad y a las bajas temperaturas, pueden almacenarse en superficies planas y abiertas. Según el tipo y la marca, los productos se colocan en pilas individuales sobre palés. Se dejan pasillos de al menos 1 m de ancho. Cerámica por cerámica y cinta por cerámica.
Cómo crear bloques de hormigón de escoria
En la actualidad, las cuestiones relacionadas con la creación de bloques de escoria en casa pueden resolverse de dos maneras.
- En el primer método, se utilizan pequeños moldes en los que se endurecen los bloques.
- En el segundo, se utiliza un equipo especial. Este equipo puede ser de fábrica o fabricarse de forma independiente, posiblemente con la participación de un tornero conocido.
Bloques de escoria en moldes
La fabricación de bloques de escoria en casa es posible utilizando formas tanto de madera como de metal. Se considera que el tamaño estándar de un bloque es de 39x19x19 cm, pero dependiendo de la finalidad del encofrado se puede fabricar casi cualquier cosa.
Los moldes constan de paredes laterales y un fondo. Si el encofrado se hace de modo que se viertan varios bloques en cada uno, se puede ahorrar mucho material.
Para que los bloques sean más ligeros y baratos, se crean huecos en ellos. Esto permite introducir botellas de vidrio en los moldes. Para facilitar su recogida, se colocan con el cuello hacia abajo. Se elimina el exceso de solución y se nivela bien el resto.
En los encofrados, los bloques se colocan durante el día y luego se sacan y almacenan en pilas bajas. Para la construcción están listos en un mes.
Equipamiento especial hormigón de escorias
Máquinas de bricolaje
La fabricación de bloques de escoria en casa de esta manera produce y garantiza una mayor calidad que Sin embargo, para ello se necesita un equipamiento especial, sobre todo una hormigonera y una vibradora.
La fabricación de la máquina requiere lo siguiente
- Utilización de chapas de acero de 2-3 mm de espesor.
- Motores asíncronos, cuya potencia es superior a 100 vatios.
- Carga para desequilibrios y vibraciones.
- Cilindros para crear huecos.
Máquina para producir bloques de hormigón de escoria.
El equipo para bloques caseros de escoria puede hacer lo siguiente
- De la chapa de acero se cortan dos rectángulos de 40×25, 2-20×25, 1-40×15, 4-4×4 y 1-39. 5×19. 5 cm.
- De los rectángulos de acero de 40×25 y 20×25 centímetros, las formas están soldadas y sus dimensiones internas corresponden a los tamaños de los bloques estándar. Sin embargo, como ya se ha dicho, los tamaños pueden variar.
- Se cortan tres piezas de un tubo de 8 cm de diámetro y 25 cm de longitud.
- Estas piezas en bruto se sueldan al encofrado mediante un rigidizador de tamaño 4×4 cm, con un rigidizador en la parte superior del mismo.
- Los vibradores se fijan al lado largo del encofrado y para ello se utilizan pernos con tuercas. El propio perno se sujeta mediante soldadura.
- Para proteger el motor del agua y la solución, se suelda una visera sobre él y se sueldan patas adicionales hasta su borde. Debido al vibrador, el centro de gravedad de toda la estructura ha cambiado, por lo que se requiere estabilidad adicional.
- El fijador se suelda al mango y el bloque de escoria ya puede pasar a la fase de fabricación.
Proceso de fabricación del bloque de escoria
Y ahora las instrucciones que explican cómo fabricar bloques de escoria en casa. Todo el proceso se divide en las siguientes etapas
Los moldes especiales diseñados para la fabricación de bloques de hormigón de escoria se llenan previamente con una solución. A continuación, se colocan en un vibrador y se encienden durante un breve periodo de tiempo. La solución precipita y añade más mezcla.
A continuación, se vuelve a encender el vibrador y se espera a que las pinzas alcancen el limitador. Esto significa que se ha completado el moldeado y, tras 5-10 segundos, preferiblemente antes de que se pare el motor, se puede retirar la forma.
El tiempo de secado del bloque acabado viene determinado por la temperatura y la humedad y oscila entre una semana y aproximadamente un mes. Ahora, sabiendo cómo hacer bloques de escoria en casa y trabajando juntos, puede dar hasta 70 piezas hasta una hora.
Bloques caseros
Para fabricar bloques caseros, es necesario determinar el tamaño futuro de los bloques. La opción más fácil para crear bloques es el uso de formas especiales.
Los bloques caseros pueden fabricarse con formas muy variadas. Esto permite utilizar los bloques tanto para el acabado de la obra como para la construcción de muros.
Se pueden utilizar diversos materiales para el relleno y también se pueden emplear ladrillos usados en su fabricación. Al crear bloques caseros, se puede controlar la densidad y resistencia del material de construcción.
Metales.
A la venta hay formas ya preparadas para la fabricación de bloques, disponibles en tamaños estándar. También puede crear sus propias formas. Necesitará preparar los siguientes materiales y herramientas
- Herramientas USHM (para cortar metal)
- Equipo de soldadura
- Papel de lija grueso
- Taladro para metal
- Metal de 5 mm de grosor
- Metal de 3 mm de grosor
En una plancha de metal de 5 mm, marca las medidas necesarias, por ejemplo 260 mm y 196 mm Deben salir cuatro detalles: una pieza rectangular de metal, una pieza rectangular de metal, una pieza rectangular de metal, una pieza rectangular de metal y una pieza rectangular de metal.
Estas piezas deben hervirse cuidadosamente en la costura interior para obtener una forma rectangular. La parte inferior no es necesario: 196 mm de ancho a los lados de la forma, que tiene que ser un mango para un uso conveniente. de una hoja de chapa de 3 mm, se debe hacer una educación vacío.
Emollage Educación es necesario:
- Ahorre solución.
- Reducción de la conductividad térmica de la pared
En el caso de las formas, 3 educación en blanco. Es necesario hacer tres espacios en blanco del tamaño adecuado, convertirlos en cilindros y hervir desde el interior.
Para unir las educaciones vacías entre sí, se debe tomar una tira de metal de 30-40 mm de ancho. Se hacen espárragos en la parte superior de las educaciones vacías y con su ayuda se sueldan los cilindros a las tiras de metal.
Hay que hacer el fondo y la tapa para el cilindro. A continuación, se suelda el mecanismo acabado a la forma. Al cortar el asa e insertar la tira metálica en el cilindro debe hervir la costura interior.
Formas de madera
Las formas para la fabricación de bloques pueden hacerse de madera. Para ahorrar tiempo en la fabricación de bloques, las formas más grandes pueden hacerse en celdas individuales.
El armazón debe hacerse sin fondo, y mediante cortes se añaden elementos intermedios. Las tiras de madera intermedias ayudan a dividir el marco de madera en el número de celdas y el tamaño necesarios.
Para retirar cómodamente el bloque de encofrado acabado, la superficie interior de la forma debe pintarse con pintura al óleo.
Preparación de la solución para los bloques
Para producir bloques de FBS, es necesario preparar la solución. Para ello, hay que tomar grava (4 partes), arena gruesa (2 partes), cemento (1 parte) y agua.
Antes de dar forma a los bloques, se pueden colocar barras de madera. Esto se solidificará y formará una ranura para el posterior moldeado. Esto ayuda a que la unión entre ellos sea más fuerte. Esto simplifica la colocación de los bloques en los cimientos. El llenado de la mezcla en los moldes se realiza sobre una superficie plana utilizando un nivel estructural.
Se seca con film y se siembra con agua durante 2 días para evitar que el producto se agriete. Antes de su uso, los bloques deben secarse bien durante 3 semanas. Durante este tiempo alcanzarán la resistencia y dureza deseadas. Asegúrese de que los rayos del sol no inciden sobre los bloques.
Equipo
Maquinaria.
En el mercado existen bastantes modelos a la venta. Hay que partir de la finalidad a la que se destina el equipo.
Construir una casa es uno, establecer tu propia pequeña producción es otro. El experto argumenta que hoy en día hay muchas actitudes nacionales y que no es aconsejable «perseguir» equipos importados. Es poco probable que el dinero gastado en él se justifique. Esto se debe a que no hay que esperar ‘superefectos’ de ellos.
¿Cuáles son las «ventajas» de adquirir equipos?
- Junto con él, se proporciona un paquete completo de documentación pertinente. Y no sólo sobre cuestiones «mecánicas», sino también sobre tecnología de producción.
- La compra incluye tanto un asesoramiento exhaustivo como asistencia técnica. Al menos durante el periodo de garantía. Los fabricantes serios han firmado acuerdos sobre el servicio postgarantía, en los que el comprador «no renuncia» al final de este periodo.
- Si se necesita algún equipo no estándar, se puede hacer un pedido especial. Será algo más caro, pero soluciona muchos problemas, ya que se necesitan tamaños diferentes durante la construcción.
Con una buena carga de trabajo, estas instalaciones se amortizan en menos de un año. Además, Vibro no sólo se utiliza para la producción de bloques de arcilla expandida. En cierto sentido, tienen un uso universal: son adecuados para la producción de bloques de escoria y muchos otros productos.
Hay varios ejemplos, no con fines publicitarios, sino sólo como «ayuda visual», para que el lector pueda orientarse en los costes de los mecanismos correspondientes.
Hefesto-1.
La instalación puede «expedir» hasta 160 productos con parámetros de 39x19x19 cm en una jornada laboral de 8 horas. No ocupa un gran espacio (0,06 m3) y con su peso (21 kg) puede trasladarse. Por sí sola, hace posible trabajar sin ayudante. La fabricación del bloque se ejecuta 1 pc. a la vez. El kit incluye una cubierta de vibración, una forma y elementos adicionales de equipamiento interno.
Hay instalaciones más productivas de esta marca y se puede realizar la fabricación simultánea de varios bloques. Pero, por supuesto, sus costes son más elevados. Por ejemplo, el precio de un producto de tres formas es de 22.900 rublos. Además, los kits cuentan con dispositivos especiales que pueden crear bloques huecos; si se necesita un dispositivo de seis formas, cuesta unos 2.000 más.
Estos son los modelos de mayor rendimiento (de 400 a 1.200 piezas por turno).
Vibraciones de la serie RMU
Se descifra como «instalaciones manuales de pequeño tamaño»; su tamaño y peso permiten transportar el producto en el maletero de un coche. La potencia no supera los 200 vatios. Funcionan con una toma monofásica normal de 220 V.
Dispositivos más baratos: se pueden utilizar piedras vibratorias (descritas aquí), pero la calidad del producto acabado será muy inferior.
Hormigoneras.
Para volúmenes de producción planificados, basta con una capacidad de tambor de 0,2 a 0,5 m3. Para la producción en «streaming», se opta por un modelo más integral.
El coste de las más baratas comienza en unos 6.000 rublos (rollos de tambor de 65-70 L). Para la construcción individual, suficiente.
Hay que tener en cuenta que el amasado manual disminuye la calidad de la composición resultante y afecta a las propiedades del bloque de arcilla expandida listo.
Además del equipamiento, se requiere lo siguiente
- Sala de producción. Requisitos — ventilación y calefacción eficaces (si se prevé organizar la producción durante el año);.
- Lugar seco para el producto (el bloque debe estar cubierto con un toldo o una película). También se requiere un «mini-almacén» si se vende.
- Suministro eléctrico industrial.
Recomendaciones
- A la hora de comprar el material, conviene comprobar si el kit incluye insertos para producir bloques huecos. Son dispositivos muy útiles.
- Es mejor si la espuma para rellenar la solución es extraíble. Esto permite liberarla y que el bloque aparezca cuando se describe la superficie.
- Para las pequeñas empresas, se recomienda comprar una línea aerodinámica que ya tenga todo lo necesario. Sin embargo, el coste medio de un conjunto de este tipo es de unos 1, 000, 000 rublos. Sin embargo, si los reúne usted mismo a partir de unidades compradas individualmente, puede reducir el coste a la mitad aproximadamente.
Se recomienda utilizar máquinas para bloquear
Antes de que el promotor decide crear bloques de hormigón de escoria de forma independiente para la construcción de muros, surge el problema de la selección del equipo. No siempre es posible alquilar máquinas para la producción de bloques de construcción, especialmente en pequeños asentamientos. Muchas personas deciden fabricar su propio equipo. Dependiendo de su función financiera, pueden ceñirse a las siguientes opciones
- El diseño más sencillo, que permite construir bloques de pared en casa con un coste mínimo.
- Una versión modernizada del equipo, con dispositivos de sellado y mecanismos adicionales.
Es difícil dar una respuesta clara, que la máquina para producir los bloques deben ser utilizados. Todo depende del número de bloques que haya que crear y de la capacidad de financiación. Analicemos la función de cada unidad.
Bloques de diseño simplificado
Para reducir y fabricar bloques de escoria por sí solos, se pueden crear unidades mecanizadas, utilizando un vibrador y sin necesidad de mecanismos adicionales. Los procesos de fabricación con tecnología simplificada pueden realizarse de forma especial.
Bloques de diseño simplificado
- Las formas se recogen y se recubren en la superficie interior con aceite usado.
- Verter la mezcla de bloques de escoria en una forma plegable.
- Dejar 3-4 horas para que la solución se endurezca.
- Desmontar el recipiente y retirar con cuidado los bloques.
- Ofrecer la posibilidad de secado en una habitación cerrada.
Si es necesario fabricar un producto hueco, se recomienda utilizar una botella de bebida ordinaria para formar la cavidad. Se pueden crear máquinas simplificadas para la producción de bloques, que son recipientes de madera o acero del tamaño necesario, con un coste mínimo.
Máquinas modernizadas para producir bloques de construcción
Debido a la necesidad de bloques de escoria para la construcción de grandes edificios, se pueden crear máquinas más complejas para producir bloques equipadas con dispositivos especiales.
- Mecanismo de vibración. Como vibrador se utiliza un motor eléctrico, en cuyo eje de accionamiento se encuentra una excéntrica. La potencia de accionamiento es de 0,5-1,5 kW, dependiendo del tamaño del encofrado y de la masa de la solución de hormigón de escoria. Bajo la influencia de la vibración, se produce la compresión de la masa de hormigón de escoria, la distribución uniforme del material por todo el espacio del encofrado y la eliminación de las inclusiones de aire. Como resultado del sellado, aumentan el peso específico y la resistencia del producto de bloque de escoria.
- Dispositivos de elevación. Destinados a acelerar la extracción del producto acabado del recipiente de conformado. Existen varias soluciones constructivas que aceleran y facilitan la toma del bloque. En la versión más sencilla, se suelda un asa de cualquier forma a la capacidad de moldeo, suficiente para extraer el bloque endurecido. Utilizando planos ya preparados, el mecanismo de palanca puede montarse independientemente a partir de materiales improvisados.
Máquinas modernizadas para producir bloques de construcción
Las formas utilizadas en esta unidad deben corresponder al tamaño del bloque de hormigón que se pretende producir. En la mayoría de los casos, se fabrican productos con dimensiones estándar de 0,4×0,2×0,2 m. La altura de la capacidad de encofrado debe aumentarse en 4m5 cm. Para simular cavidades en el fondo del recipiente, se pueden soldar recortes de tubería del diámetro requerido.
Equipamiento industrial
El equipo más pequeño para producir bloques de hormigón en casa es la presencia de una forma y prensa. Las cubetas de construcción son adecuadas para la preparación del hormigón, mientras que las palas soviéticas sirven para dosificar el material y mezclar la masa. De hecho, este conjunto es suficiente para 20-40 bloques moldeados por turno, y con tal ritmo de producción se construirá una casa o un garaje sólido sólo al cabo de 6-8 meses.
Se puede utilizar una pequeña herramienta de mecanización por encofrad o-una prensa vibratoria eléctrica- para mejorar la producción, ¡y una hormigonera de 120-140 litros puede aumentar la productividad! Desde luego, aquí hay que buscar una obra más grande para poder utilizar toda la gama de equipos de producción de bloques de hormigón.
Para iniciar un negocio de éxito en la producción de materiales de construcción, no sólo es necesario para fabricar grandes volúmenes de producto, sino también para ofrecer a los consumidores un surtido que es diferente de la gama de sus competidores. Para ello, establezca la liberación de muros de carga, piezas, tabiques y materiales de bloque no estándar. Es posible crear un surtido de este tipo utilizando herramientas industriales para producir bloques de hormigón. Normalmente, la configuración de la instalación incluye contenedores para la preparación de soluciones, prensas vibratorias y paneles de control. La propia instalación puede ser móvil, de modo que tras la producción de una forma, puede trasladarse a otro lugar para que los bloques empiecen a secarse.
En el caso de las minifábricas, se utilizan equipos con un alto grado de automatización y una proporción reducida de mano de obra física. La producción de bloques de hormigón requiere una mezcladora en una sala separada con preparación de soluciones, contenedores de encofrado y equipos climáticos para acelerar el proceso de secado. Además, el funcionamiento de la línea requiere también una línea de envasado y un almacén para guardar el producto listo para su envío al consumidor.
Si se prevé crear bloques de hormigón celular, es necesario complementar la producción con un autoclave para secar el material a presión. La línea en este caso permite la producción de hormigón celular de una forma y finalidad específicas, proporcionando al cliente un conjunto de bloques listo para la construcción de una casa o un garaje.
Tipos de productos de hormigón
Estos encofrados se dividen en cuatro tipos, en función del tipo utilizado para fabricar el hormigón
Sector pesado.
Para la producción de esta variedad de bloques de hormigón, se añade grava o piedra triturada a la composición, lo que aumenta su resistencia. Se utilizan para construir cimientos.
Encofrados porosos ligeros
Para su producción se utiliza cemento Portland y rellenos porosos (por ejemplo, arcilla expandida). Suelen utilizarse como material para muros.
Bloques porosos ligeros
Móvil.
El proceso de fabricación da como resultado una forma de hormigón de bajo coste, ya que en la producción no se utiliza el proceso de autoclave.
Silicato.
La producción de estas variedades se caracteriza por el uso obligatorio del proceso de tratamiento en autoclave. Además, la cal y las arenas de cuarzo están inevitablemente presentes en estos productos. A partir de hormigones de silicato se pueden fabricar formas pesadas cuando se añade un gran número.
Fecha de actualización: 11-20-2023
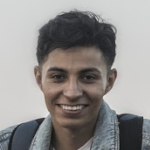
Este tema está cerrado para la publicación de respuestas.